Predictive Maintenance for Industrial Equipment
Home » Case Study » Predictive Maintenance for Industrial Equipment
Project Overview:
Objective
Predictive Maintenance is our focus as a leading data collection and annotation company. We specialize in providing diverse datasets, including images, videos, texts, and speech, to empower machine learning models. In this project, our aim was to utilize our expertise to predict maintenance needs for industrial equipment effectively. By integrating data analytics, sensors, and advanced technology, we anticipated equipment failures, enabling timely and strategic interventions.
Scope
Our project embraced the broad spectrum of predictive maintenance for industrial equipment. This included both continuous and periodic monitoring, leveraging our state-of-the-art sensors and IoT devices. These tools, combined with our advanced data analytics and machine learning capabilities, were pivotal in identifying potential equipment failures.
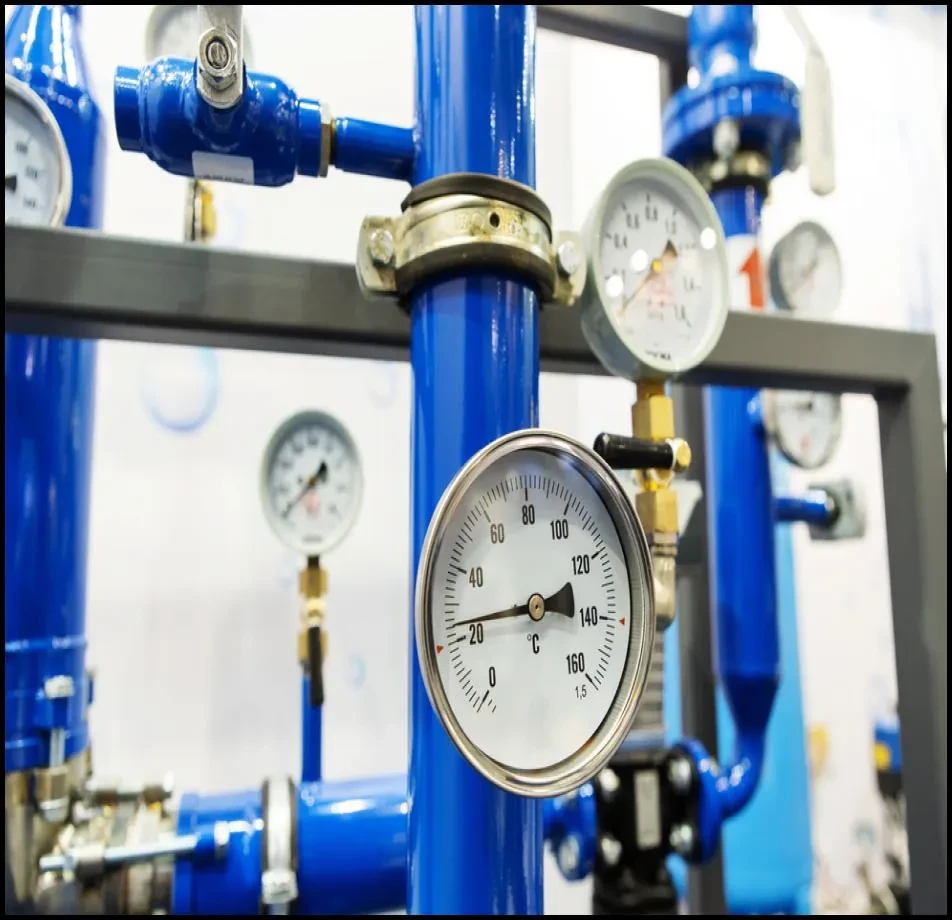
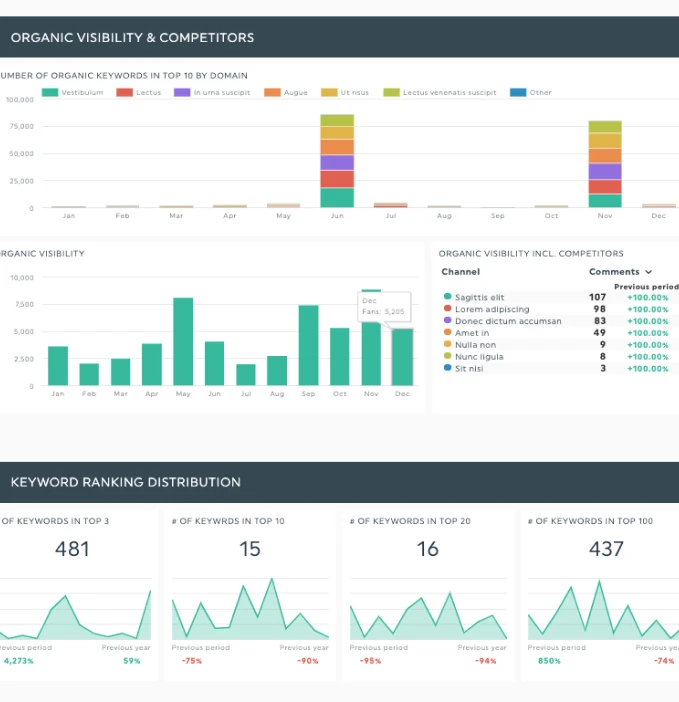
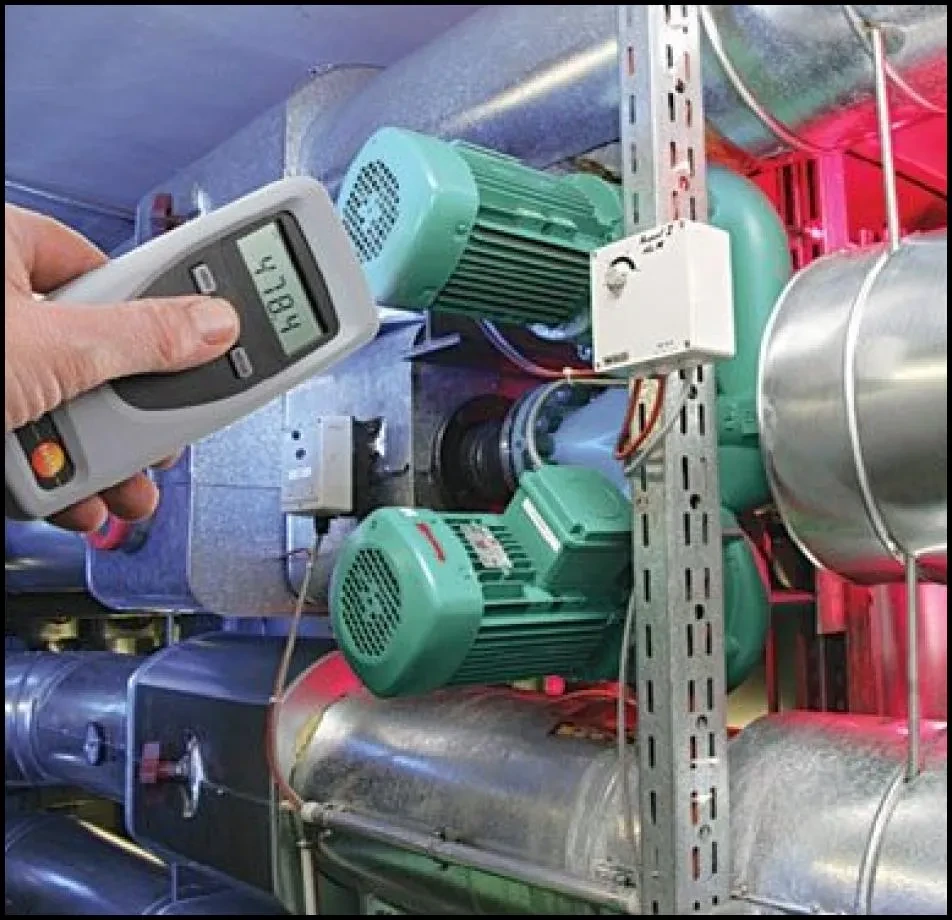
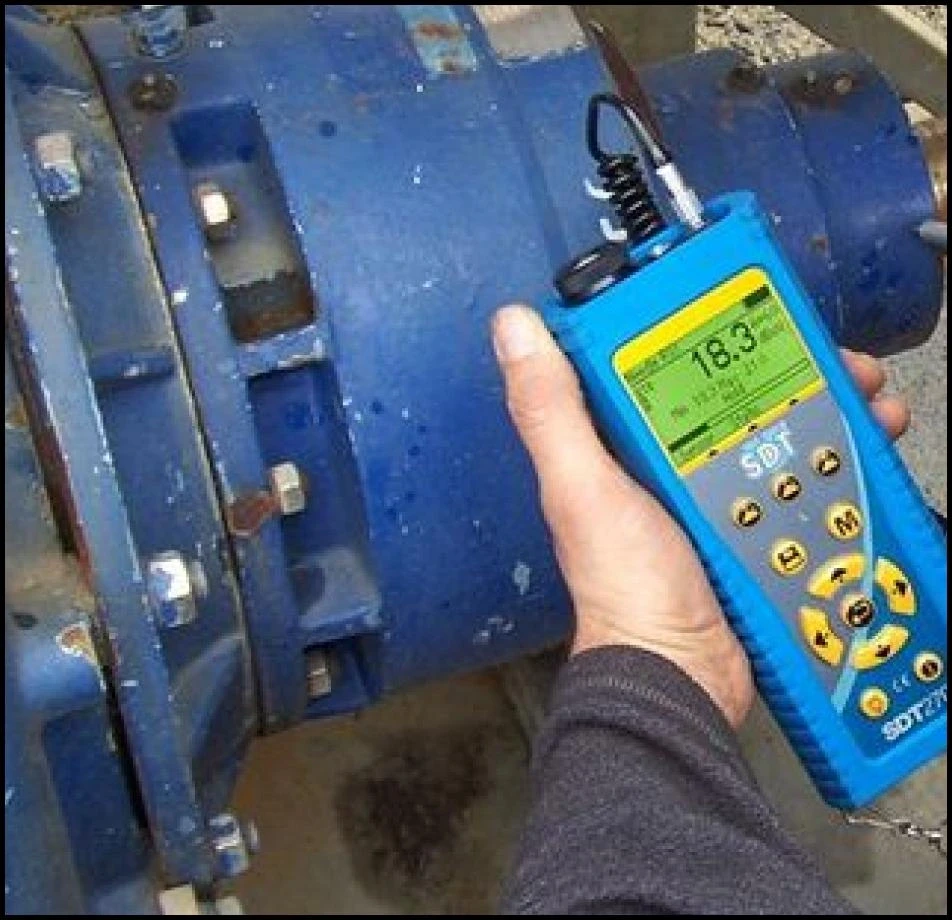
Sources
- Data Collection Instruments: Sensors, IoT devices, and monitoring systems gather real-time information on equipment health and performance.
- Historical Databases: Past records, maintenance logs, and equipment lifecycle data offer invaluable insights into patterns and potential failure modes.
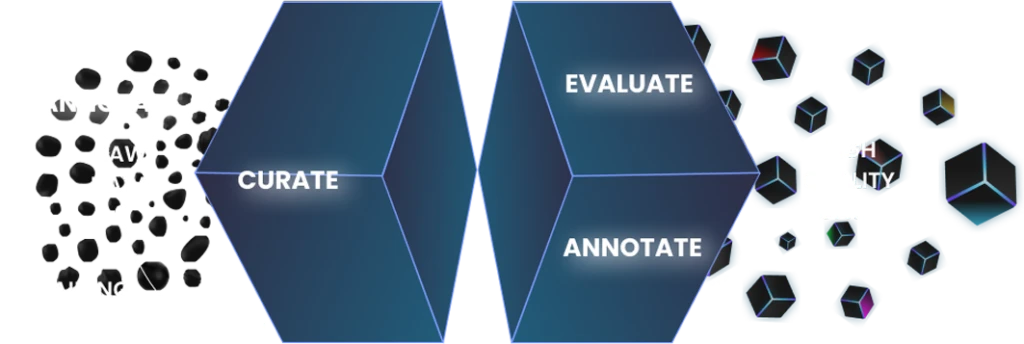
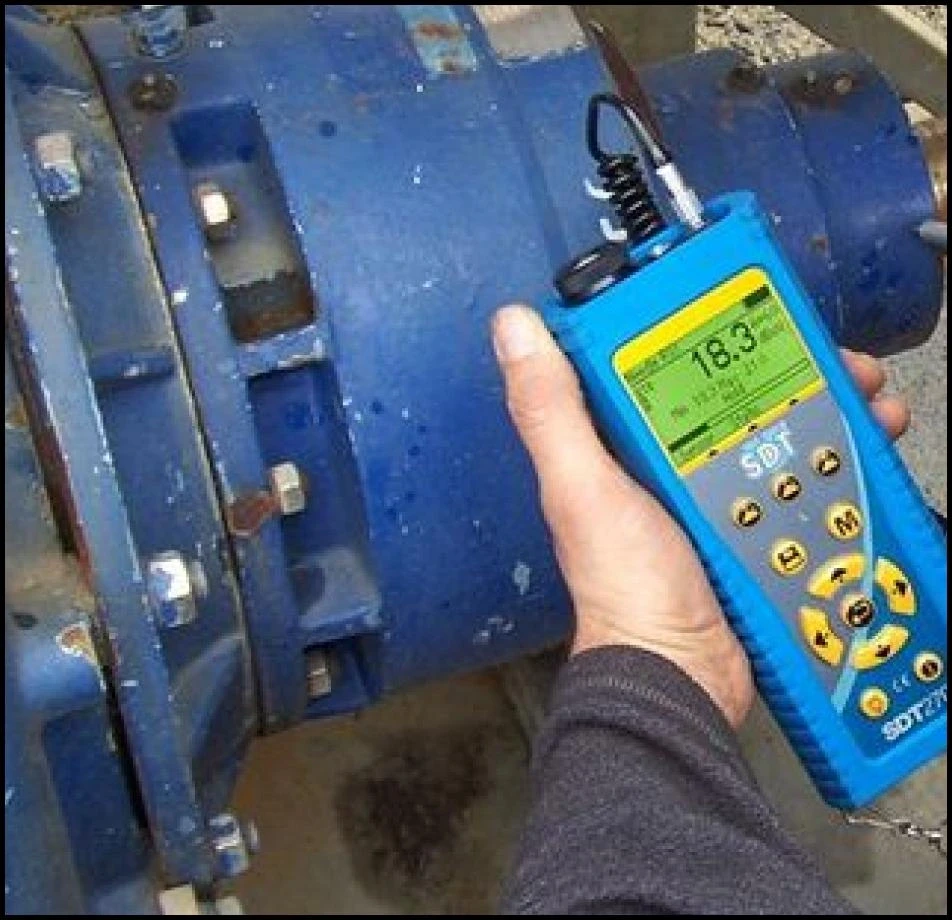

Data Collection Metrics
- Operational Metrics: Measures like vibration, temperature, and RPM.
- Failure Indicators: Deviations in power consumption or efficiency.
Annotation Process
Stages
- Data Collection: Gather real-time equipment metrics.
- Analysis: Interpret and find patterns in collected data.
- Prediction: Forecast potential equipment failures.
- Intervention: Schedule and execute timely maintenance.
- Feedback: Refine models based on maintenance outcomes.
Annotation Metrics
- Precision: Accuracy of the identified relevant data points.
- Recall: Proportion of actual relevant points captured.
- F1-Score: Harmonic mean of precision and recall, balancing the two metrics.
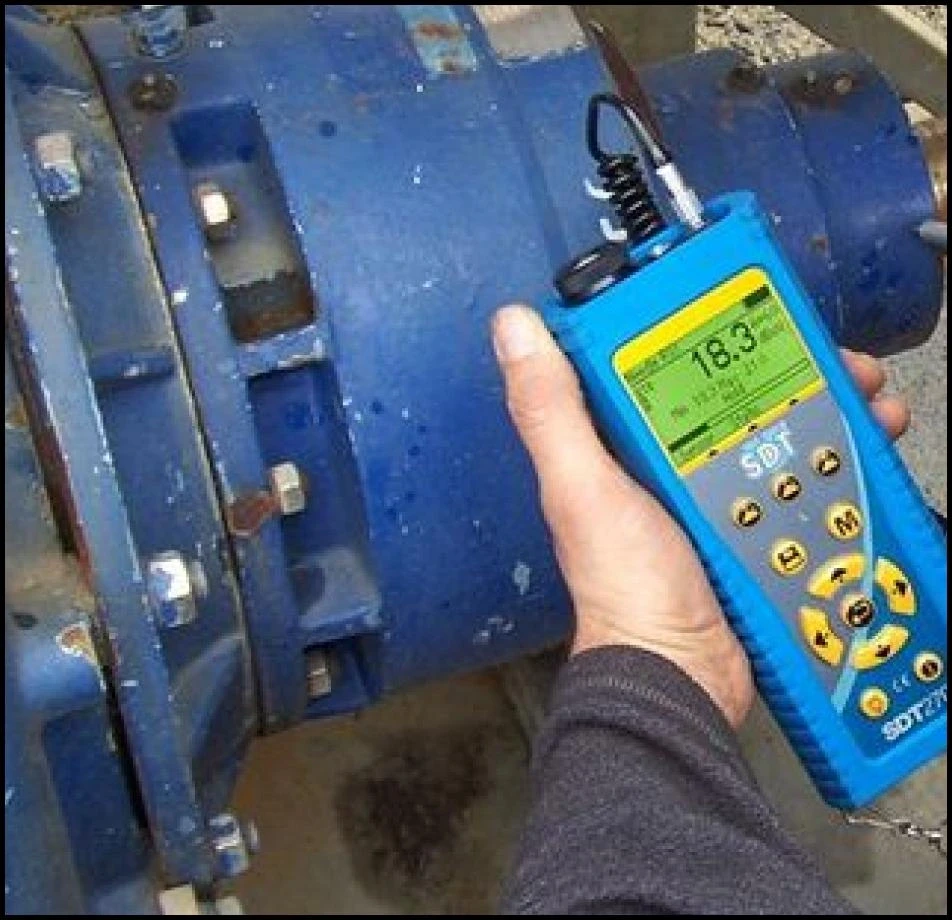
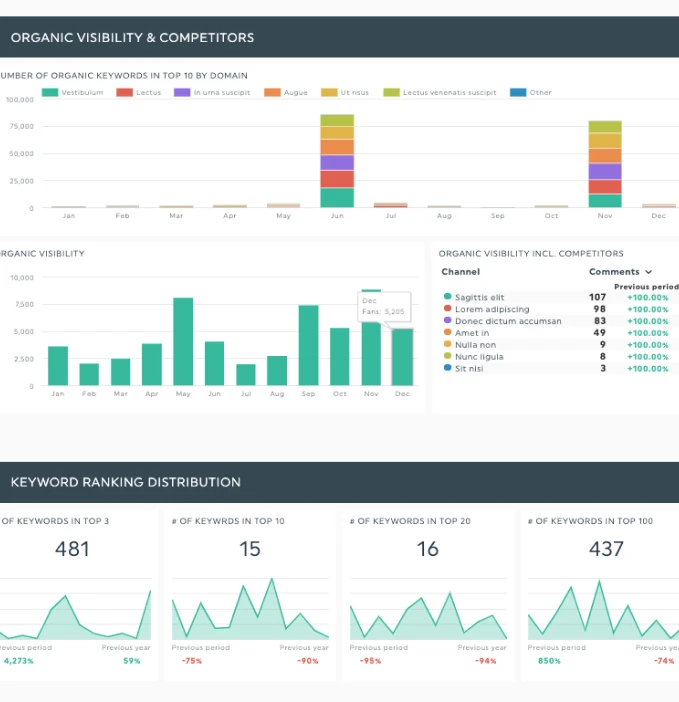
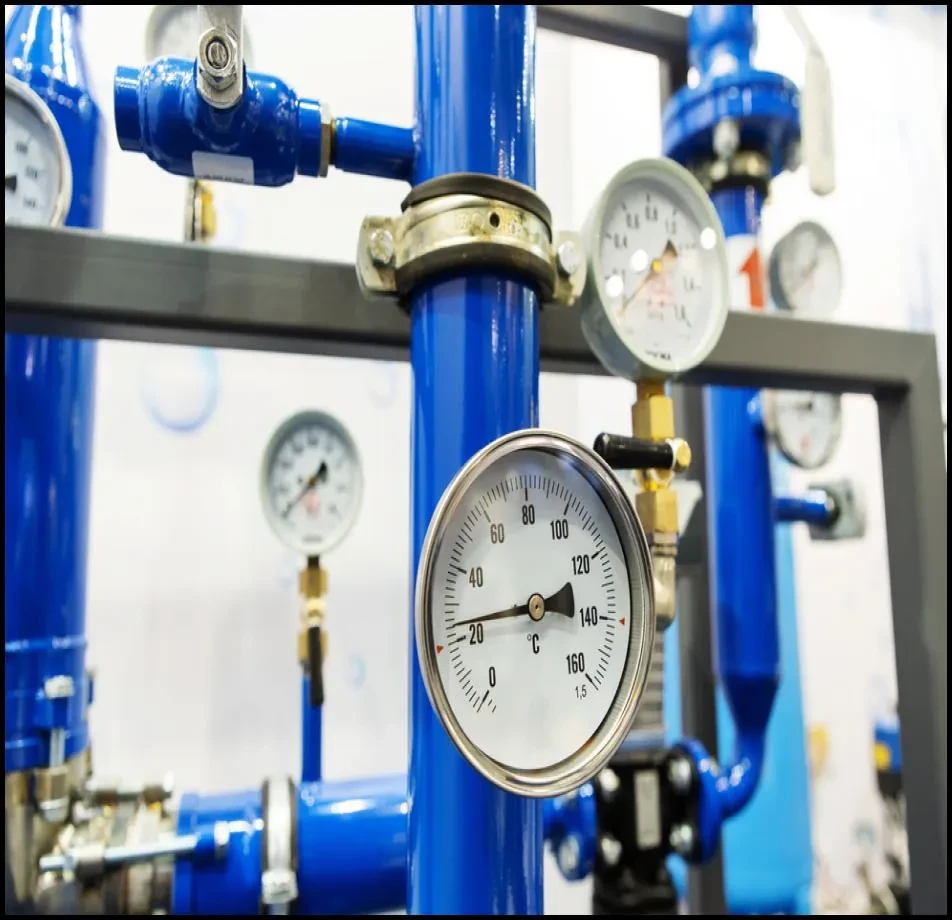
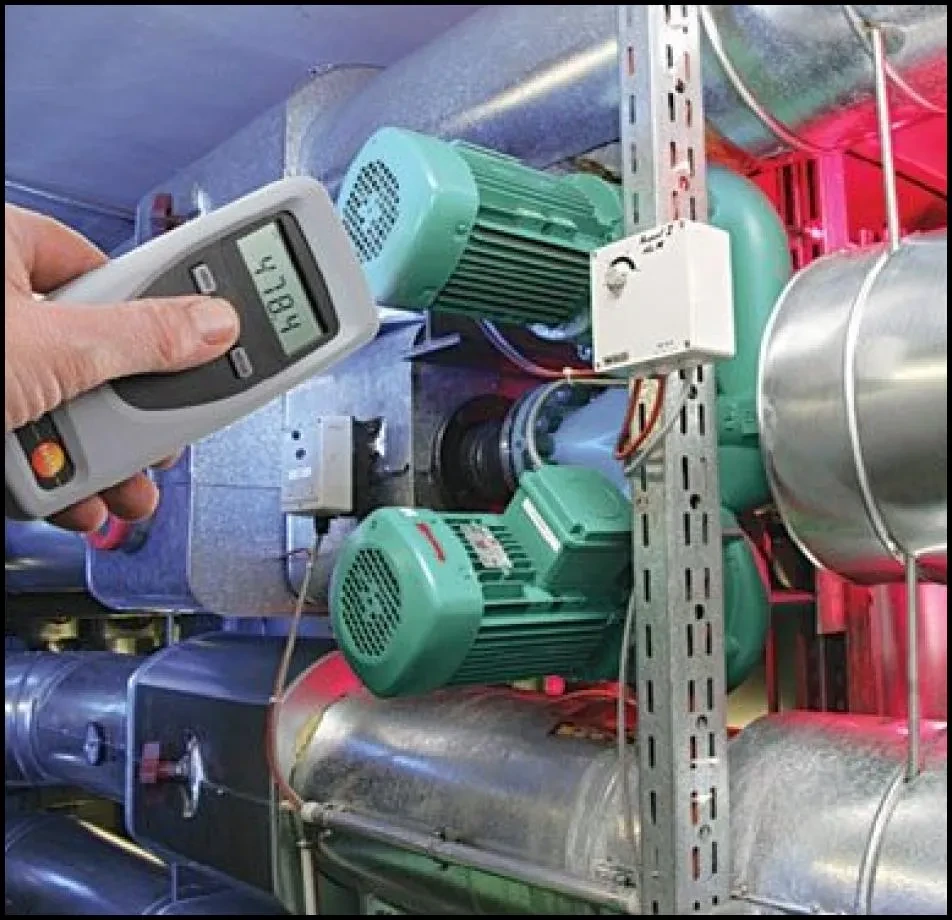
Quality Assurance
Stages
Validation Protocols: Rigorous testing to ensure data accuracy and system reliability.
Data Encryption: Protecting sensitive information from unauthorized access.
Access Controls: Restricting data access to authorized personnel only.
QA Metrics
- Defect Density: Number of defects per unit of software size.
- Test Pass Rate: Percentage of tests passed successfully.
Conclusion
Predictive maintenance (PdM) for industrial equipment harnesses data-driven techniques to anticipate and prevent equipment failures,  to significant cost savings, reduced downtimes, and increased operational reliability.

Quality Data Creation

Guaranteed TAT

ISO 9001:2015, ISO/IEC 27001:2013 Certified

HIPAA Compliance

GDPR Compliance

Compliance and Security
Let's Discuss your Data collection Requirement With Us
To get a detailed estimation of requirements please reach us.